Pavement Design for Airfields - indexChapter 1 Introduction - ufc_3_260_020017Use of Flexible PavementsSoil StabilizationFigure 1-1. Typical flexible pavement structureFigure 1-3. Typical flexible pavement with stabilized baseChapter 2 Army Airfield/Heliport RequirementsArmy Aircraft Design Loads and LevelsRoller-Compacted Concrete Pavement - ufc_3_260_020024Figure 2-1. Typical layout of traffic areas for Army Class III and IV airfieldsChapter 3 Air Force Airfield and Aggregate Surfaced Helicopter Slide Areas and Heliport RequirementsMedium-load and modified heavy-load airfieldType B Traffic AreasAircraft Design Loads for Air Force PavementsDesign Pass Level for Air Force PavementsTable 3-1 Design Gross Weights and Pass Levels for Airfield PavementsTable 3-2 Gradation for Aggregate Surface Courses (Percent Passing)Table 3-4 Frost Design Soil ClassificationTable 3-5 Frost Area Soil Support Indices (FASSI) of Subgrade SoilsTable 3-6 Gradation for Aggregate Surface Courses (Percent Passing)Table 3-7 Compaction Requirements for Helicopter Pads and Slide AreasSurface Drainage - ufc_3_260_020037Figure 3-1. Typical layout of traffic areas for Air Force light-load and auxiliary airfield pavementsFigure 3-2. Typical layout of traffic areas for Air Force mediumFigure 3-3. Typical layout of traffic areas for Air Force heavy-load airfield pavementsFigure 3-4. Aggregate surfaced design curves for helicoptersChapter 4 Navy and Marine Corps Airfield RequirementsAircraft LoadingsTable 4-1 Aircraft Characteristics and Design LoadingsTable 4-1 Aircraft Characteristics and Design Loadings - Cont'dRoller-Compacted Concrete Pavement - ufc_3_260_020046Pavement Design PolicyFigure 4-1. Primary, secondary, and supporting traffic areas for NavyFigure 4-2. landing Gear AssembliesChapter 5 Site InvestigationsTable 5-1 Soil Sampling and Testing StandardsSelect Material and Subbase for Flexible PavementsSoil Compaction TestsFigure 5-1. Typical boring logFigure 5-2. Typical soil profileFigure 5-3. Approximate relationships of soil classification and soil strengthChapter 6 SubgradeLaboratory TestsSubgrade Modulus of Soil ReactionTable 6-1 Typical Values of Modulus of Soil ReactionSubgrades with CBR values above 20Table 6-2 Compation Requirements for Coshesive Sugrades and Select Materials Under Flexible Pavements - Air Force PavementsTable 6-3 Compation Requirements for Cohesioless Sugrades and Select Materials Under Flexible Pavements - Air Force PavementsTable 6-4 Compation Requirements for Cohesive Sugrades and Select Materials Under Flexible Pavements - Air Force PavementsTable 6-5 Compation Requirements for Cohesionless Sugrades and Select Materials Under Flexible Pavements - Air Force PavementsTable 6-6 Compaction Requirements for Navy and marine Corps Flexible PavementsTable 6-7 Compaction Requirements for ShouldersTreatment of Problem SoilsStabilized SubgradesFigure 6-1. Procedure for Determining Laboratory CBR of Subgrade SoilsFigure 6-2. Selection of design subgrade CBR using in-place testsChapter 7 Select Materials and Subbase Courses For Flexible PavementsTable 7-1 Minimum Unconfined Compressive Strength for Cement, Lime, Lime-CementSeparation LayersChapter 8 Aggregated Base CoursesBlast Furnace SlagAggregate Base Course for Army and Air Force Rigid PavementTable 8-2 Gradations for Lean Concrete Base MaterialsStrength of Aggregate Base Courses for Flexible PavementsTable 8-3 Minimum Surface and Aggregate Base-Course Thickness RequirementsMinimum Surface and Aggregate Base-Course Thickness RequirementsTable 8-6 Aggregate Base-Course Minimum Thickness Requirements for NavyCompaction Requirements for Army Figure 8-1. Effect of base-course thickness on modulus of soil reaction for nonfrost conditionsChapter 9 Pavement MaterialsTerminologyMechanismsDurabilityPortland-Cement Stabilization DurabilityBituminous Stabilization - ufc_3_260_020091Portland-Cement Concrete ReinforcingSpecial Air Force RequirementSpecial Airfield Exposure ConditionsSpecification and ConstructionAsphaltic ConcreteMix Design - ufc_3_260_020098Recycled MaterialsTable 9-1 Types of Portland CementChapter 10 Flexible Pavement Design - CBR MethodAdditional Considerations for Thickness DesignDesign Examples - ufc_3_260_020103Design Examples - Cont'dStabilized Pavement SectionsTable 10-1 Example Design Using Mixed TrafficTable 10-1 Example Design Using Mixed Traffic - Cont'dSpecial AreasTable 10-2 Equivalency Factors for Army and Air Force PavementsArmy AirfieldsJuncture Between Rigid and Flexible PavementsFigure 10-1. Flexible pavement design curves for Army Class I heliports and helipadsFigure 10-2. Flexible pavement design curves for Army Class II and V heliports and helipadsFigure 10-3. Flexible pavement design curves for Army Class III airfields as defined in paragraph 4.c of Chapter 2Figure 10-4. Flexible pavement design curves for Army Class IV airfields Figure 10-5. Flexible pavement design curves for Army Class IV airfieldsFigure 10-6. Flexible pavement design curves for Army Class IV airfieldsFigure 10-7. Flexible pavement design curves for Army Class IV airfields Figure 10-8. Flexible pavement design curves for Navy and Marine Corps single-wheel aircraft, primary and secondary traffic areasFigure 10-9. Flexible pavement design curve for Navy and Marine Corps dual-wheel aircraft, primary traffic areasFigure 10-10. Flexible pavement design curve for Navy and Marine Corps dual-wheel aircraft, secondary traffic areasFigure 10-11. Flexible pavement design curve for Navy and Marine Corps C-130, primary traffic areasFigure 10-12. Flexible pavement design curve for Navy and Marine Corps C-130, secondary traffic areasFigure 10-13. Flexible pavement design curve for Navy and Marine Corps C-141, primary traffic areasFigure 10-14. Flexible pavement design curve for Navy and Marine Corps C-141, secondary traffic areasFigure 10-15. Flexible pavement design curve for Navy and Marine Corps C-5A, primary traffic areasFigure 10-16. Flexible pavement design curve for Navy and Marine Corps C-5A, secondary traffic areasFigure 10-17. Flexible pavement design curve for Air Force light-load airfieldFigure 10-18. Flexible pavement design curve for Air Force medium-load airfieldFigure 10-19. Flexible pavement design curve for Air Force heavy-load pavementFigure 10-20. Flexible pavement design curve for Air Force modified heavy-load pavementFigure 10-21a. Flexible pavement design curve for Air Force C-130 assault landing zone airfieldFigure 10-21b. Flexible pavement design curve for Air Force C-17 assault landing zone airfieldFigure 10-22. Flexible pavement design curve for Air Force auxiliary airfield, type A traffic areasFigure 10-23. Flexible pavement design curve for Air Force auxiliary airfield, types B and C traffic areasFigure 10-24. Flexible pavement design curve for shoulders on Army and Air Force pavementsFigure 10-25. Air Force flexible pavement design curve for F-15, type A traffic areasFigure 10-26. Air Force flexible pavement design curve for F-15, types B and C traffic areasFigure 10-27. Air Force flexible pavement design curve for C-141, type A traffic areasFigure 10-28. Air Force flexible pavement design curve for C-141, types B, C, and D traffic areasFigure 10-29. Air Force flexible pavement design curves for B-1, type A traffic areasFigure 10-30. Air Force flexible pavement design curve for B-1, types B, C, and D traffic areasFigure 10-31. Air Force flexible pavement design curve for B-52, type A traffic areasFigure 10-32. Air Force flexible pavement design curve for B-52, types B, C, and D traffic areasChapter 11 Layer Elastic Design of Flexible PavementsTable 11-1 Temperature Data for Jackson, MississippiTraffic volume Aircraft loadingMaterial Characterization - ufc_3_260_020149Subgrade soilsTable 11-2 Typical Poisson's Ratios for Four Classes of Pavement MaterialsAsphalt Strain CriteriaConventional Flexible Pavement DesignPavements With a Stabilized Base CourseExample Design for Conventional Flexible PavementTable 11-3 Bituminous Concrete Moduli for Each Month for Conventional Flexible Pavement Design BasedTable 11-4 Bituminous Concrete Moduli for Each Month for Conventional Flexible Pavement Design BasedTable 11-5 Grouping Traffic into Traffic Groups According to Similar Asphalt ModuliTable 11-6 Structure Data File for Input into the JULEA Computer ProgramTable 11-7 Results of Computer Runs for the Example ProblemStep 5 - Computation of Damage FactorsTable 11-8 Data File for Computing Subgrade Damage for Pavement Thicknesses of 840, 760Table 11-9 Program Output for Subgrade Damage for Pavement Thicknesses of 840, 760Table 11-10 Data File for Computing Asphalt DamageTable 11-11 Program Output for Asphalt DamageTable 11-12 Bituminous Concrete Moduli for Each Month for ABC Pavement Design BasedTable 11-13 Bituminous Concrete Moduli for Each Month for ABC Pavement Design Table 11-14 Data for Computing Damage Factors for Taxiway DesignTable 11-15 Data for Computing Damage Factors for Runway DesignFigure 11-1. Temperature relationships for selected bituminous concrete thicknessFigure 11-2. Computation of effective gear print for single gearFigure 11-3. Computation of effective gear print for twin gearFigure 11-4. Computation of repetition factor for tandem gearFigure 11-5. Design criteria based on subgrade strainFigure 11-7. Flow diagram of important steps in design of bituminous concrete pavementFigure 11-8. Relationship between cracked section modulus and unconfined compressive strengthFigure 11-9. Flow diagram of important steps in design of pavements having chemically stabilized base courseFigure 11-10. Flow diagram of important steps in design of pavements having stabilized baseFigure 11-11. Estimation of resilient modulus MRFigure 11-12. Results of laboratory tests for dynamic modulus of bituminous concreteFigure 11-13. Section for pavement thickness of 760 millimeters (30 inches) for initial taxiway designFigure 11-14. Section for pavement thickness of 610 millimeters (24 inches) for initial runway designFigure 11-15. Pavement design for taxiwaysFigure 11-16. Design for runwaysFigure 11-17. Design for asphalt concrete surfaceFigure 11-18. Computed strain at the top of the subgrade for taxiway designFigure 11-19. Damage factor versus pavement thicknessFigure 11-20. Computed strain at the bottom of the asphalt for taxiway designFigure 11-21. Computed strain at the top of the subgrade for runway designFigure 11-22. Computed strain at the bottom of the asphalt for runway designChapter 12 Plain Concrete PavementsExamples of Plain Concrete Pavement Design for Army and Air ForceExamples of Plain Concrete Pavement Design for Army and Air Force - Cont'dExample Design, Slab on Stabilized BaseExample problem solutionTable 12-1 Example of Mixed Traffic DesignStructural Slab Cracking from Aircraft LoadingsTable 12-2 Stress-Strength Ratios and Allowable CoveragesThickness design procedure for a single design aircraftTable 12-3 Fatigue Damage Summary Sheet for Mixed TrafficTable 12-4 Pass-to-Coverage RatiosDesign Examples for Navy and Marine Corps Plain Concrete Pavements Subgrade evaluation and testingJoint UsesTable 12-5 Design Example for Primary (Channelized) Traffic AreasTable 12-5 Design Example for Primary (Channelized) Traffic Areas - Cont'dTable 12-6 Design Example for Primary (Unchannelized) Traffic Areas - Cont'dTable 12-6 Design Example for Primary (Unchannelized) Traffic Areas - Cont'd Joints for Army and Air Force PavementsWidth and depth of sealant reservoirTable 12-7 Recommended Spacing of Transverse Contraction JointsTable 12-8 Dowel Size and Spacing for Construction, Contraction, and Expansion JointsBetween pavement and structuresJoint For Navy and Marine Corps PavementContraction (Weakened Plane) JointsJoint SealantsJointing Pattern For Rigid Airfield Pavements Expansion Joints and Slip JointsTied Joints (Navy Only)Sample Joint LayoutsSample Joint Layouts - Cont'd - ufc_3_260_020221Sample Joint Layouts - Cont'd - ufc_3_260_020222Figure 12-1. Plain concrete design curves for Army Helipads, Class IFigure 12-2. Plain concrete design curves for Army Class II airfieldsFigure 12-3. Plain concrete design curves for Army Class III airfields as defined in paragraph 4.c of Chapter 2Figure 12-3. Plain concrete design curves for Army Class IV airfields (C-130 Aircraft) With Runway 1,525 Meters (5,000 Feet)Figure 12-5. Plain concrete design curves for Army Class IV airfields (C-17 Aircraft) With Runway 2,745 Meters (9,000 Feet)Figure 12-6. Plain concrete design curves for Air Force light-load pavementsFigure 12-7. Plain concrete design curves for Air Force medium-load pavementsFigure 12-8. Plain concrete design curves for Air Force heavy-load pavementsFigure 12-9. Plain concrete design curves for Air Force modified heavy-load pavementsFigure 12-10. Plain concrete design curves for Air Force C-130 assault landing zone pavementsFigure 12-11. Plain concrete design curves for Air Force C-17 assault landing zoneFigure 12-12. Plain concrete design curves for Air Force auxiliary pavementsFigure 12-13. Plain concrete design curves for F-15 aircraftFigure 12-14. Plain concrete design curves for C-141 aircraftFigure 12-16. Plain concrete design curves for B-1 aircraftFigure 12-17. Plain concrete design curves for shouldersFigure 12-18. Example of allowable passes determinationFigure 12-20. Rigid pavement thickness design chart for P-3 aircraft (Navy)Figure 12-21. Rigid pavement thickness design chart for C-130 aircraft (Navy)Figure 12-22. Rigid pavement thickness design chart for C-141 aircraft (Navy)Figure 12-23. Rigid pavement thickness design chart for C-5A aircraft (Navy)Figure 12-24. Chart for determining flexural stress for single-wheel gear (Navy)Figure 12-25. Chart for determining flexural stress for P-3 aircraft (Navy)Figure 12-26. Chart for determining flexural stress for C-130 aircraft (Navy)Figure 12-27. Chart for determining flexural stress for C-141 aircraft (Navy)Figure 12-28. Chart for determining flexural stress for C-5A aircraft (Navy)Figure 12-29. Typical jointingFigure 12-30. Contraction joints for plain concrete pavementsFigure 12-31. Joint sealant details for plain concrete pavements (Sheet 1 of 3)Figure 12-31. (Sheet 2 of 3)Figure 12-31. (Sheet 3 of 3)Figure 12-32. Construction joints for plain concrete pavements (Sheet 1 of 3)Figure 12-32. (Sheet 2 of 3)Figure 12-32. (Sheet 3 of 3)Figure 12-33. Expansion joints for plain concrete pavementsFigure 12-34. Slip joints for plain concrete pavementsFigure 12-35. Rigid-Flexible Pavement Junction (Army of Air Force)Figure 12-36. Rigid-Flexible Pavement JunctionFigure 12-37. PCC to AC joint detail (removal and construction)Figure 12-38. PCC to AC joint detail (very little traffic expected)Figure 12-39. Sample jointing pattern (SI units)Figure 12-40. Sample jointing pattern (metric units)Figure 12-41. Sample Jointing Pattern for 180-ft.Wide Lanes Figure 12-42. Sample jointing pattern at an intersectionFigure 12-43. Effects of confusion in sawing jointsChapter 13 Reinforced Concrete Pavement DesignReduced Thicknes Design - Army and Air ForceReinforcemnt to Control Pavement CrackingMismatched JointsReinforced Concrete Pavements in Frost AreasJointing - ufc_3_260_020273Assume that a 152-millimeter (6-inch) lean concrete base course will be usedTable 13-1 Reinforced Concrete Pavement Design ExampleTable 14-1 Reinforced Concrete Pavement Design Example on a Lean Concrete Base CourseFigure 13-1. Reinforced concrete pavement designFigure 13-2. Typical layouts showing reinforcement of odd-shaped slabsFigure 13-2. (Concluded)Figure 13-3. Reinforcing steel details (Continued)Figure 13-3. (Concluded)Figure 13-4. Contraction joints for reinforced concrete pavementsFigure 13-5. Construction joints for reinforced concrete pavements (Sheet 1 of 4)Figure 13-5. Construction joints for reinforced concrete pavements (Sheet 2 of 4)Figure 13-5. Construction joints for reinforced concrete pavements (Sheet 3 of 4)Figure 13-5. Construction joints for reinforced concrete pavements (Sheet 4 of 4)Figure 13-6. Expansion joints for reinforced concrete pavementsChapter 14 Fibrous Concrete Pavement DesignAllowable Deflection for Fibrous Concrete PavementExample of Fibrous Concrete Pavement DesignFigure 14-1. Fibrous concrete pavement design curves for UH-60Figure 14-2. Fibrous concrete pavement design curves for CH-47Figure 14-3. Fibrous concrete pavement design curves for C-130Figure 14-4. Fibrous concrete pavement design curves for Air Force light-load airfieldsFigure 14-5. Fibrous concrete pavement design curves for Air Force medium-load airfieldsFigure 14-6. Fibrous concrete pavement design curves for Air Force heavy-load airfieldsFigure 14-7. Fibrous concrete pavement design curves for Air Force modified heavy-load airfieldsFigure 14-8. Fibrous concrete pavement design curves for Air Force shortfield airfieldsFigure 14-9. Fibrous concrete pavement design curves for shouldersFigure 14-10. Deflection curves for UH-60Figure 14-11. Deflection curves for CH-47Figure 14-12. Deflection curves for C-130Figure 14-13. Deflection curves for Air Force light-load pavementsFigure 14-14. Deflection curves for Air Force medium-load pavementsFigure 14-15. Deflection curves for Air Force heavy-load pavementsFigure 14-16. Deflection curves for Air Force modified heavy-load pavementsFigure 14-17. Deflection curves for Air Force shortfield pavementsFigure 14-18. Deflection curves for shoulder pavementsFigure 14-19. Allowable Deflection Curve for Fiberous Concrete PavementsFigure 14-19. Allowable Deflection Curve for Fiberous Concrete Pavements - Cont'dChapter 15 Continuously Reinforced Concrete Pavement DesignReinforcing Steel DesignTerminal DesignExample of Continuously Reinforced Concrete Pavement DesignExample of Continuously Reinforced Concrete Pavement Design - Cont'dExample of Continuously Reinforced Concrete Pavement Design - Cont'd Figure 15-1. Details of a wide-flange beam jointChapter 16 Prestressed Concrete Pavement DesignDesign Procedure - ufc_3_260_020319Design Procedure - Cont'dPrestressed Tendon Design - ufc_3_260_020321 Prestressing Steel TendonsJointing - ufc_3_260_020323Examples of Prestressed Concrete Pavement DesignPrestressed Tendon Design - ufc_3_260_020325Prestressed Tendon Design - Cont'dFigure 16-1. Stress repetitions versus load repetition factorFigure 16-2. A/R2 versus load-moment factorFigure 16-3. Ratio of multiple wheel gear to single-wheel gear load versus A/R2Figure 16-4. Typical section of transverse jointsFigure 16-5. Typical transverse joint seals (Sheet 1 of 3)Figure 16-5. (Sheet 2 of 3)Figure 16-5. (Sheet 3 of 3)Figure 16-6. Thickness versus design prestressChapter 17 Overlay Pavement DesignSite Investigations - ufc_3_260_020336Preparation of Existing PavementCondition of Existing Concrete PavementRigid Overlay of Existing Rigid PavementPlain Concrete Overlay - ufc_3_260_020340Example of Plain Concrete Overlay DesignReinforced Concrete OverlayReinforced Concrete Overlay - Cont'dContinuously Reinforced Concrete OverlayPrestressed Concrete Overlay of Rigid PavementAll-Bituminous OverlayReflective CrackingTable 17-1 Pass per Coverage RatiosNonrigid Overlay on Flexible PavementAs an example of the overlay design procedureOverlays in Frost RegionsFigure 17-1. Structural condition index versus condition factorFigure 17-2. Factor for projecting cracking in a flexible pavementFigure 17-3. Location guide for the use of geotextiles in retarding reflective crackingChapter 18 Rigid Pavement Inlay DesignRigid Inlays In Existing Rigid PavementFigure 18-1. Typical rigid pavement inlay in existing flexible pavementFigure 18-2. Typical rigid pavement inlay in existing rigid pavementChapter 19 Layer Elastic Design of Rigid PavementsMaterial Characterization - ufc_3_260_020360Bound Bases (Subbases)Table 19-1 Recommended Maximum Stress Levels to Test Bituminous-Stabilized MaterialsMaterial requirementModulus and Poisson's ratioDesign Criteria - ufc_3_260_020365Frost ConsiderationBase Slab Pavement Fatigue and Structural ConditionReinforced ConcreteDesign Examples - ufc_3_260_020369Design Example 1, Single AircraftTable 19-3 Computation of Cumulative Damage for Selected Pavement Sections, Granular BasesTable 19-5 Characteristics of Design AircraftTable 19-6 Computation of Cumulative Damege for Mixed Traffic, 10-inch Stabilized Base CourseTable 19-7 Relationship Between Cumulative Damage and PCC Thickness for Mixed TrafficDesign Example 4, Alternate Overlay Design ProcedureTable 19-8 Data for Overlay Design, Example 4 (Base Slab Calculations)Table 19-9 Time Intervals for the 356-millimeter (14-inch) OverlayTable 19-10 Computation of the Cumulative Damage for the 14-inch OverlayTable 19-10 Computation of the Cumulative Damage for the 14-inch Overlay - Cont'dFigure 19-1. Diagram for Design of Airfield Rigid Pavements Figure 19-2. Correlation between resilient modulus of elasticityFigure 19-3. Relationship between SCI and coverages at initial crackingFigure 19-4. Base slab performance curveFigure 19-6. Overlay thickness versus logarithm of timeFigure 19-8. Relationship between cumulative damageFigure 19-9. Relationship between cumulative damage and pavement thicknessFigure 19-10. Base slab performance curve for the 356-millimeter (14-inch) overlayFigure 19-11. Actual performance curve with the 356-millimeter (14-inch) overlay in placeFigure 19-13. Results of the analysis performed on the 305-, 356Chapter 20 Seasonal Frost ConditionsTable 20-1 Frost Design ClassificationTable 20-2 Frost Susceptibility ClassificationTable 20-3 Frost Area Soil Support Indexes (FASSI) for Subgrade SoilsControl of surface roughness in overrunsIt is good practice to use a combined base thickness equal in thickness to the slabLimited Subgrade Frost Penetration MethodLimited Subgrade Frost Penetration Method - Cont'd - ufc_3_260_020397Limited Subgrade Frost Penetration Method - Cont'd - ufc_3_260_020398Granular Base and Subgrade-Course RequirementsDrainage Layer RequirementsDepth of Subgrade PreparationControl of Differential Heave at Drains, Culveerts, Ducts, Inlets, Hydrants, and LightsPavement Thickness TransitionsCompaction - ufc_3_260_020404Example 2. Design a type A traffic area on an ArmyRigid Pavement Design Examples for Seasonal Frost ConditionsExample 1. Design an Air Force medium-load pavementLimited subgrade frost penetration design - ufc_3_260_020408Limited subgrade frost penetration design - Cont'd - ufc_3_260_020409 Example 2. Design an Air Force heavy-load pavement airfieldReduced subgrade designLimited subgrade frost penetration design - ufc_3_260_020412Limited subgrade frost penetration design - cont'd - ufc_3_260_020413Subgrade preparationSubgrade preparation - Cont'dFigure 20-1. Frost area index of reaction (FAIR) for design of rigid pavementsFigure 20-2. Determination of freezing indexFigure 20-3. Distribution of design freezing indexes in North AmericaFigure 20-4. Distribution of mean freezing indexes in Northern EurasiaFigure 20-5. Frost penetration beneath pavementsFigure 20-6. Design of combined base thickness for limited subgrade frost penetrationFigure 20-7. Placement of drainage layer in frost areasFigure 20-8. Tapered transition used where embankment material differs from natural subgrade in cutFigure 20-9. Subgrade details for cold regionsFigure 20-10. Transitions for culverts beneath pavementsFigure 20-11. Relationship between base course thickness and PCC thickness for example 1Figure 20-12. Relationship between base course thickness and PCC thickness for example 2Chapter 21. Improving SKid Resistance/Reducing Hydroplaning Potential Of Runways Porous Friction Surfaces.Figure 21-1. Groove configuration for airfieldsAppendix B: Airfield/Helicopter Design Analysis Outline Site Description Results Of Investigations And Testing Pavement Thickness Design Criteria Drainage Design - ufc_3_260_020443Construction Materials List of Required Waivers Appendix C: Recommended Contract Drawing Outline For Airfield/Heliport Pavements Phasing Plan and Details Pavement Removal Plan Paving Plan - ufc_3_260_020449Plan and Profile Sheets Reinforcing Details Appendix D: Waiver Processing Procedures Additional RequirementsAir Force: Navy and Marine CorpsObtaining WaiverAppendix E: Determination pf Flexural Strength and Modulus Of Elasticity Of Bituminous Concrete Test Procedures Report Appendix F: Curves For Determining Effective Strain Repetitions Figure F-2. Effective repetitions of strain for UH-60 aircraft, type A or primary traffic areasFigure F-3. Effective repetitions of strain for CH-47 aircraft, types B, C, or secondary traffic areasFigure F-4. Effective repetitions of strain for CH-47 aircraft, type A or primary traffic areasFigure F-5. Effective repetitions of strain for OV-1 aircraft, types B, C, or secondary traffic areasFigure F-6. Effective repetitions of strain for OV-1 aircraft, type A or primary traffic areasFigure F-7. Effective repetitions of strain for C-12 aircraft, types B, C, or secondary traffic areasFigure F-8. Effective repetitions of strain for C-12 aircraft, type A or primary traffic areasFigure F-9. Effective repetitions of strain for C-130 aircraft, types B, C, or secondary traffic areasFigure F-10. Effective repetitions of strain for C-130 aircraft, type A or primary traffic areasFigure F-11. Effective repetitions of strain for F-15 aircraft, Air Force types B and C traffic areasFigure F-12. Effective repetitions of strain for F-15 aircraft, Air Force type A traffic areasFigure F-13. Effective repetitions of strain for F-14 aircraft, types B, C and secondary traffic areasFigure F-14. Effective repetitions of strain for F-14 aircraft, type A or primary traffic areasFigure F-15. Effective repetitions of strain for B-52 aircraft, types B, C or secondary traffic areasFigure F-16. Effective repetitions of strain for B-52 aircraft, type A or primary traffic areasFigure F-17. Effective repetitions of strain for B-1 and C-141 aircraft, types B, C, or secondary traffic areasFigure F-18. Effective repetitions of strain for B-1 and C-141 aircraft, type A or primary traffic areasFigure F-19. Effective repetitions of strain for P-3 aircraft, types B, C, or secondary traffic areasFigure F-20. Effective repetitions of strain for P-3 aircraft, type A or primary traffic areasFigure F-21. Effective repetitions of strain for C-5 aircraft, types B, C, or secondary traffic areasFigure F-22. Effective repetitions of strain for C-5 aircraft, type A or primary traffic areasAppendix G Procedure For Aration of Bituminous Cylindrical SpecimensProcedure - ufc_3_260_020483Appendix H Procedure for Determining the Dynamic Modulus of Bituminous Concrete MixturesProcedure - ufc_3_260_020485CalculationsAppendix I Procedure for Estimating the Modulus of Elasticity of Bituminous Concrete Corrected Aggregate Volume ConcentrationFigure I-1. Relationship between penetration at 25 degrees C and ringFigure I-2. Nomograph for determining the stiffness modulus of bitumensAppendix J Procedure for Determining the Modulus of Elasticiity of Unbound Granular and Subbase Course MaterialsRelationshipsFigure J-1. Relationships between modulus of layer n and modulus of layer n + 1 for various thicknesses of unbound base courseFigure J-2. Modulus values determined for first exampleAppendix K Procedure for Determining the Flexural Modulus and Fatigue Characteristics of Stabilized SolisTest ProcedureFatigue characteristicsFigure K-1. General view of equipment setupFigure K-3. Miscellaneous detailsAppendix L Procedure for Determining Resilient Modulus of Subgrade MaterialCohesive Soils Containing Negligible Amounts of GravelCohesionless Soils Containing Negligible Amounts of GravelSoils Containing GravelQ Test With Back-Pressure SaturationChamber PressureEquipment - ufc_3_260_020506Preparation of Specimens and Placement in Triaxial Cell - ufc_3_260_020507Resilience Testing of Cohesive soilsResilience Testing of Cohesionless SoilsInterpretation of Test Results Special ConsiderationsFigure L-1. Schematic diagram of typical triaxial compression apparatusFigure L-2. Triaxial cellFigure L-3. LVDT clampsFigure L-4. Presentation of results of resilience tests on cohesive soilsFigure L-5. Presentation of results of resilience tests on cohesionless soilsFigure L-6. Estimated deviator stress at top of subgradeFigure L-7. Determination of subgrade modulus for cohesive soilsFigure L-8. Relationship for estimating 2 due to overburdenFigure L-9. Estimated at Top of SubgradeFigure L-10. Selection of Mr for Silty-Sand Subgrade with Estimated Thickness of 762 MillimetersAppendix M Procedure for Determining the Fatigue Life of Bituminous ConcreteSpecimen PreparationReport and Presentation of ResultsFigure M-1. Repeated Flexure ApparatusFigure M-2. Initial mixture bending strain versus repetitions to fracture in controlled stress testsFigure M-3. Provisional fatigue data for bituminous base-course materialsAppendix N Procedure for Determining the Resilient Modulus of Granular Base MaterialEnd PlatensPreparation of Specimens and Placement in Triaxial Cell - ufc_3_260_020530Placement of LVDT Measurement ClampsComputations and Presentation of ResultsPresentation of ResultsFigure N-1. Triaxial cell used in resilience testing of granular base materialFigure N-2. Schematic of frictionless cap and baseFigure N-3. Details of Top LVDT ring clampFigure N-4. Details of bottom LVDT ring clampFigure N-5. Representation of results of resilience test on cohesionless soils
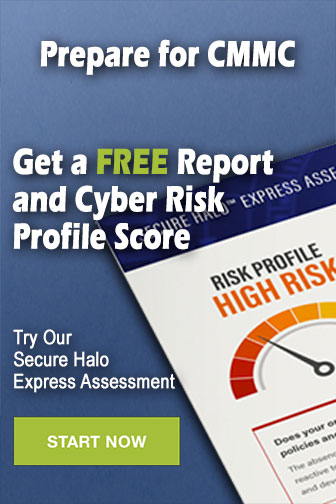