Pile Driving Equipment - indexChapter 1: Introduction - ufc_3_220_020012Table 1-1. Timber Pile SpecificationsFigure 1-1. Cross Section of a Concrete Post-tensioned Cylinder PileTable 1-2. Precast Concrete Pile SpecificationsSheet PilesTable 1-3. Steel Pipe Pile SpecificationsTable 1-4. Concrete Cast in Shell Driven with MandrelTable 1-5. Concrete Cast in Shell Driven without MandrelTable 1-6. Steel HP Section PilesTable 1-7. Helical Steel PilesTable 1-8. Composite PilesTable 1-9. Expanded Base PilesMaterial SpecificationsGeneral Installation MethodFigure 1-2. Typical pile shoesFigure 1-2. Typical pile shoes (concluded)Chapter 2: Factors for Design and ConstructionObstructions - ufc_3_220_020029Table 2-1. Quick Guide to Selection of Pile Driving EquipmentVibratory Hammers - ufc_3_220_020031Figure 2-1a. Preliminary Method for Sizing Hammers for Concrete and Steel PilesFigure 2-1a. (Concluded)Figure 2-1b. Preliminary Method for Sizing Hammers for Concrete and Steel Piles, Metric UnitsFigure 2-1b. (Concluded)Figure 2-2a. Method for Sizing Vibratory Hammers, Metric UnitsFigure 2-2a. (Concluded)Figure 2-2b. Method for Sizing Vibratory Hammers, English UnitsFigure 2-2b. Method for Sizing Vibratory Hammers, English Units (Concluded)Vibratory Hammers - ufc_3_220_020040Table 2-4a. Amplitude Requirements, Metric UnitsTable 2-4b. Amplitude Requirements, English UnitsDesign VerificationEconomy of PilesPile Driving Analyzer - ufc_3_220_020045The Bearing GraphSelection and Timing of Load TestsConstructionPile Installation - ufc_3_220_020049Site ConstructibilityHandling and Lofting PilesSplicingFigure 2-3. Typical splices for pilesFigure 2-3. Typical splices for piles (Concluded)Sequence of InstallationCare and Maintenance Chapter 3: EquipmentDriving AccessoriesVibratory DriversSheet PilingCranes for Impact HammersHydraulic Impact HammersSwinging LeadersMethods and Limitations of JettingConcrete Pile CuttingTable 3-1. Strengths and Weaknesses of Impact Hammer TypesTable 3-1. Strengths and Weaknesses of Impact Hammer Types -Cont.Table 3-1. Strengths and Weaknesses of Impact Hammer Types (Concluded)Table 3-2a. Instruction for Use of Hammer TablesTable 3-2b. Hammer Chart, Metric UnitsTable 3-2b. Hammer Chart, Metric Units -Cont. - ufc_3_220_020071Table 3-2b. Hammer Chart, Metric Units -Cont. - ufc_3_220_020072Table 3-2b. Hammer Chart, Metric Units -Cont. - ufc_3_220_020073Table 3-2b. Hammer Chart, Metric Units -Cont. - ufc_3_220_020074Table 3-2b. Hammer Chart, Metric Units(Concluded)Table 3-2c. Hammer Chart, English UnitsTable 3-2c. Hammer Chart, English Units -Cont. - ufc_3_220_020077Table 3-2c. Hammer Chart, English Units -Cont. - ufc_3_220_020078Table 3-2c. Hammer Chart, English Units -Cont. - ufc_3_220_020079Table 3-2c. Hammer Chart, English Units -Cont. - ufc_3_220_020080Table 3-2c. Hammer Chart, English Units (Concluded)Table 3-3. Summary of cushion material characteristicsTable 3-4. Advantages and disadvantages of fixed leadersTable 3-6. Advantages and underhung leadersFigure 3-2. Idealized hammer force-time curveFigure 3-4. Typical single-acting air/system hammerFigure 3-6. Stroke changing device for air/steam hammersFigure 3-7b. Interior view of air/ateam hammerFigure 3-8. Typical differential-acting air/steam hammerFigure 3-9. Operating cycle for differential-acting air/steam hammersFigure 3-10. Typical hydraulic hammerFigure 3-11. Pile jacking deviceFigure 3-12. Operating diagram of diesel hammerFigure 3-13. Typical open-end diesel hammerFigure 3-14. Typical closed-end diesel hammerFigure 3-15. Cushion configurationsFigure 3-16. Typical driving helmetsFigure 3-17. Mandrel for shell pilesFigure 3-18. Eccentrics for vibratory hammersFigure 3-19. Low-frequency vibratory hammerFigure 3-20. Medium frequency vibratory hammerFigure 3-22. Commercial crane pile driving rigFigure 3-23. Boom point connectionsFigure 3-24. Fixed leadersFigure 3-25. Moonbeam spotter leaderFigure 3-28. Swinging leaderFigure 3-29. Swinging leader with batter pilesFigure 3-30. Underhung leaderFigure 3-31. Impact hammer with pantsFigure 3-32. Hammer extension (top view)Figure 3-34. Jet configurationsFigure 3-35. Underwater hydraulic impact hammerFigure 3-37. Bucket for plug removalFigure 3-38. Pile beaverChapter 4: Monitoring of Pile InstallationFigure 4-1. Lubrication points, air/steam hammerTable 4-1. Do' and do not' of VIbratory HammersDirect Energy MonitoringPile Installation - ufc_3_220_020119Pile Driving Analyzer - ufc_3_220_020120Prevention of Pile Damage During DrivingTable 4-2. Indicators of pile damageGood Driving PracticeComplicationsDriving Equipment and PilesObstructions - ufc_3_220_020126Permafrost AreasMethod of InstallationChapter 5: Pile Driving in Coral Sands (Case History)Soil InvestigationsTable 5-1. Summary of load test resultsUltimate Pile CapacitySupplemental Test ProgramLessons Learned - ufc_3_220_020134Establish Criteria for and Complete Load TestsFigure 5-2. Pile group layout with batter pile orientationsFigure 5-3. Standard penetration resistance resultsFigure 5-4. Piling embedment depthsFigure 5-6. Wave equation analysis resultsFigure 5-7. Pile capacity by Meyerhof and Nordlund methodsFigure 5-7. Pile capacity by Meyerhof and Nordlund methods -Cont.Figure 5-7. Pile capacity by Meyerhof and Nordlund methods (Concluded)Figure 5-9. Penetration resistance of production piles during restrikeFigure 5-10. Computation of axial pile compressionFigure 5-11. Computation of pile toe settlementFigure 5-13. Comparison of driving record of indicator pile with piles E-2 and S-5-12Figure 5-14. Blow count comparison for restruck piles
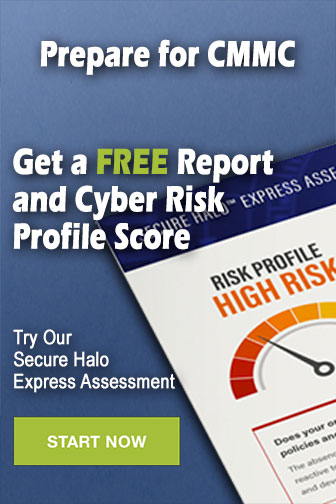